Creating safe, sustainable products: The effort matters because people matter


Troy Virgo
Director of sustainability and product stewardship
Shaw Industries
We spend an average of 90% of our time indoors, according to reports from the US EPA, the EU and others. With that sobering statistic in mind, it’s important that the places where we live, work, learn, heal and spend the vast majority of our time are safe and healthy.
Sustainability efforts for companies around the world are shifting beyond environmental, ecological and planetary concerns, to those intrinsically focused on people.
In the past several years, we’ve seen the creation of the WELL Building Standard, with a stated mission to improve human health and wellbeing in buildings and communities throughout the world; a focus on material health as part of the latest iteration of the US Green Building Council’s LEED certification (LEED v4); and a proliferation of new certifications or standard reporting tools to assess or disclose chemical ingredients. And in the past year, The Home Depot, Target and others have unveiled chemical strategies with a strong underpinning on human health.
Discussions that were previously limited to technical conferences or solely focused on food, cosmetics and consumer products are now becoming mainstream within the built environment sector. It’s an area that Shaw has been focused on for the past two decades. We are committed to Cradle to Cradle principles, which include a focus on material health and the ingredients that go into our products, and also align our product chemical management efforts with BizNGO’s Principles for Safer Chemicals. Today, our sustainability efforts include an ever broadening range of human health-related topics, from asthma and allergy to acoustics and sound abatement.
Everyone should have access to safe, sustainable products for their homes and workspaces. To that end, manufacturers can lead the way by overcoming the challenges inherent in:
Knowing what’s in a product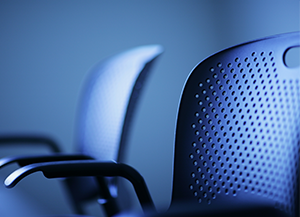
Multiple design and product development groups are going at full speed to create innovative products. This can sometimes mean there’s a focus on function and performance that may not account for human health considerations. Limited product stewardship resources to contribute to product design or ingredient selection decisions are additional challenges that many manufacturers face.
At Shaw, our intent is to know as much about our products as possible. It begins with the choices made on the raw materials to be used to make these products. We educate and train all our technical development groups to use an enterprise-wide raw material approval process and partner with our sourcing groups to ensure purchase orders are not issued without completing this review process.
We use the Cradle to Cradle Certified Products Program material health assessment methodology to characterise the hazards of chemicals present in a product and to assess any relevant routes of exposure to hazardous chemicals during the intended (and highly likely unintended) use and end-of-use phases of a product’s lifecycle. Chemical composition data for materials is needed down to the 100 ppm level (0.01%) to generate full assessment ratings. This programme’s material health rating system was developed to identify the continuum of risk — from those chemicals that pose the greatest hazard to those that pose little to no hazard.
We follow this internal approval process for all new raw materials as well as hazard screening and risk assessment, regardless of whether the final product is pursuing or already certified to the Cradle to Cradle Certified Products Program standard.
Seeking third-party certification
The growing marketplace expectation for manufacturers to be more transparent about the footprint of their manufacturing processes and the materials used to make their products has created some tensions between a desire to know what’s in a product and the need to protect intellectual property. At the same time, we often hear “I’m not a toxicologist. A list of ingredients doesn’t meaningfully tell me if the product is safe.” Without robust third-party verification of this data, there is scepticism of what information is disclosed as possibly being greenwashing.
To that end, Cradle to Cradle certification – with its focus not only on material health, but material reutilisation, renewable energy, water and social fairness – is key to our approach to creating safe, sustainable products.
Implementing sustainable sourcing policies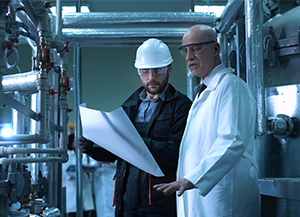
A raw material approval and chemical screening process is only as good as the information upon which it is based. Language, culture, time zone differences, non-standard forms, and a desire to protect proprietary information can make getting full ingredient composition from the supply chain a challenge.
We strive to ensure that the products we source from others are held to the same high standards we set for our own operations, and our global sourcing group is an active participant in this effort. Shaw’s sustainable sourcing policy advances our efforts to improve material health by requiring transparency and disclosure around identified chemicals of concern in alignment with our commitment to Cradle to Cradle principles. We require, through purchase agreements, that our raw material and finished goods suppliers disclose the presence of any chemicals on the Cradle to Cradle Banned List or that are classified as carcinogenic, mutagenic and reproductive toxins.
An easy-to-understand sustainable sourcing policy and focus on fostering relationships is critical for success. In-person facility tours and other engagement efforts strengthen relationships and open dialogue. This helps ensure suppliers understand why the requirements and preferences outlined are important to their customers and the larger industry.
An added benefit to this leadership effort is that changes in how suppliers disclose information and (when necessary) reformulate products stand to not only benefit one company and its customers, but possibly others the supplier serves as new options for safer chemistry become more widely available.
Engaging product R&D and design teams
Product design and development efforts are typically focused on new products or functional or performance improvements to existing products. It can be difficult for a manufacturer to get limited resources committed to changing the chemistry of already commercialised products that are meeting customer expectations. Yet this can often be a great source of health improvement.
Every company’s structure and decision-making processes are different. It’s
critical to understand who influences a product’s design and what information and priorities are driving those decisions. Several years ago, we were able to reformulate a flagship product in a way that had no impact on performance, reduced operational costs, and lessen the chemical hazard profile of the product, all by challenging conventional wisdom of whether added materials were delivering the intended effect in the finished product.
As with supplier relationships, it’s critical for product research and development, design teams and others to understand why sourcing or chemical policies, standard operating procedures and other actions are in place. It helps clarify the risks and the rewards – so each role can support the creation of innovative products to meet ever-changing customer needs and minimise unintended consequences.
While these steps are rather straightforward, it’s hard work and requires constant collaboration and innovation. That collaboration has to take place across multiple disciplines and departments and with a broad range of external partners (suppliers, NGOs, academics and other businesses facing similar challenges) in unprecedented ways as new information, formulations and technology are available and as customer preferences and other business dynamics shift.
While the Earth is fairly resilient, we have the responsibility to help it remain hospitable for the people living on it. The effort matters, because people matter.